Haryana - Panja Durries
- Nidhi Shegokar
- Aug 30, 2023
- 2 min read
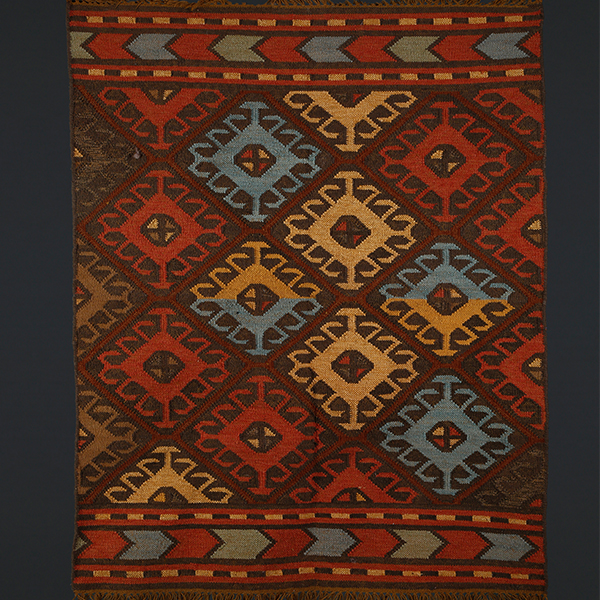
Panja weaving is an integral part of India's rich weaving heritage, primarily employed in creating durries, lightweight woven rugs for floor covering. The technique's name stems from the local dialect's term "panja," which refers to a claw-like tool made of metal. This tool is instrumental in beating and securing the threads in the warp during the weaving process.
The history of Panja weaving traces back to ancient times, with early carpet weaving being documented in Indian Buddhist texts around 500 B.C. Carpets similar to modern Persian and Anatolian styles were also utilised in Mongolia. The craft gained prominence during the Mughal era in the 16th century when the emperors imported and supported Persian artisans, who, in turn, trained Indian weavers in carpet making. Over time, Indian weavers developed their own designs and styles under the patronage of Mughal rulers like Akbar and Shahjehan, leading to remarkable carpet creations.
The practice of Panja weaving extends across India, from Jammu and Kashmir to Tamil Nadu, and from Rajasthan to Arunachal Pradesh. It's worth noting that the craft's connection to caste is limited, with weavers hailing from diverse backgrounds. The weaving process involves the use of both cotton and wool threads. Cotton is predominantly used for the warp, while wool serves as the weft material. Different types of wool, including handspun and mill-spun, are employed based on the type of dye used.
The tools utilised in Panja weaving encompass the taana machine, which consists of a rotating horizontal cylinder and a vertical frame for thread rolls. The loom frame features movable vertical beams to hold the warp, and a reed keeps the threads aligned. The essential panja, resembling a claw, is crucial for beating the weft threads into the warp. Weavers use a charkha to prepare yarn bundles for the weft.
During the weaving process, weavers sit at the loom and carefully follow designs to create the patterns. After weaving each row of weft, the panja is used to secure the threads tightly. The warp layers are adjusted using a mechanism called kamana and rich, enhancing the durability of the finished durrie. Once weaving is complete, the master weaver oversees finishing, which might involve washing, knitting loose ends, and trimming protruding threads.
Panja-woven durries find various applications, including flooring, seating mats, and upholstery. The craft's historical significance and the intricate techniques employed contribute to India's enduring tradition of weaving excellence.